Products
PatrolSuite
PatrolSuite is MAP’s web-based, multi-lingual platform designed for large companies with the need to standardize quality system activities at multiple plants, on multiple continents, with multiple currencies, around the world.
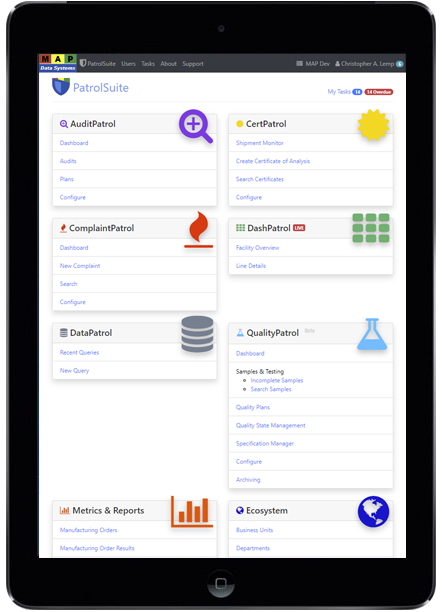
Need to run 20+ manufacturing facilities, collecting over one million test results each month, on one single instance of your quality system? No problem. This is software for large manufacturers.
The “My Tasks” page provides users with one place to go to see all tasks assigned to them by any PatrolSuite module, including the need to provide approvals. Hyperlinks take the user directly to the task requiring their attention. Due dates are clear and past-due warnings are provided. Managers can see all actions assigned to their direct reports, including those that are past-due.
“Our yields increased by about 20% at the plants where we deployed PatrolSuite.”
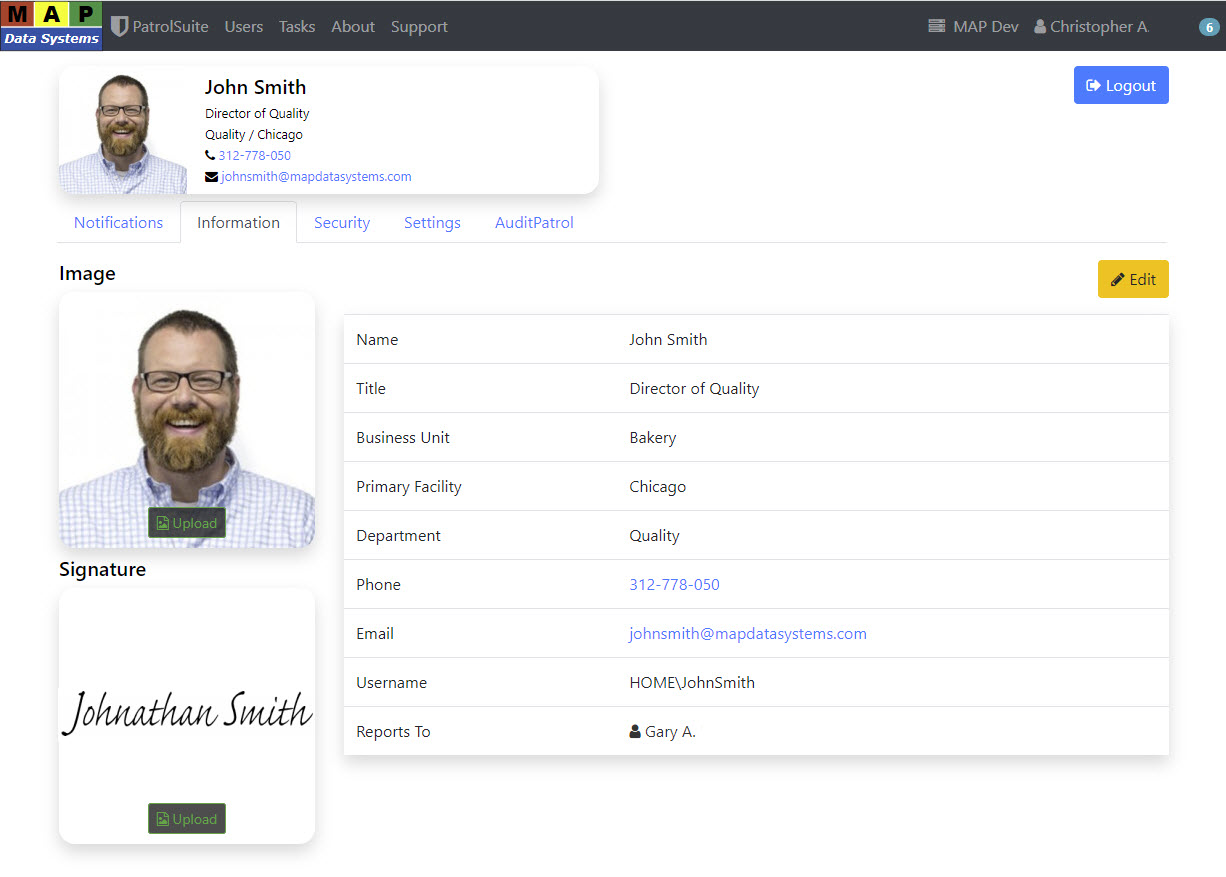
PatrolSuite is designed to be integrated with, and to communicate bi-directionally with, other CCE (critical, complex, enterprise) business systems such as the local or cloud-based ERP, MES, and HMI/SCADA systems.
PatrolSuite is mobile-friendly and can run on a Microsoft or Linux operating system. Robust maintenance and diagnostic capabilities are provided for web server management and data archiving.
“Our new CEO hired two global consulting firms to assess our manufacturing systems and recommend better solutions. Both firms recommended replacing nearly all of our manufacturing systems except our quality software (QualityPatrol) which they said is adding huge value to our business.”
QualityPatrol
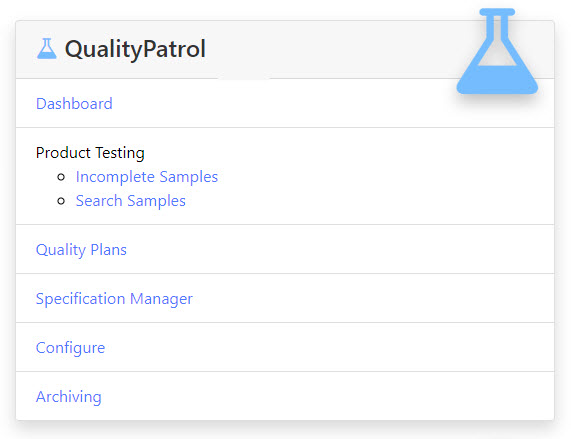
QualityPatrol enables management of the product quality plan, including test methods, test plans, specifications, sampling frequencies, and product certification requirements. Products with similar testing requirements can be organized into testing groups to minimize test plan management. RESTful APIs allow data to be automatically collected from laboratory test equipment.
The multi-tiered specifications structure allows specs to be defined at the test method, product, customer, and customer ship-to levels. A robust audit trail automatically captures spec changes.
When a sample is initiated, QualityPatrol tells the user what tests are required, what test methods to use, and enables the user to record the results. Out of specification results are highlighted. Quality state management can be integrated with the local ERP or MES to automatically approve product for further processing, or to place product on hold when out of specification conditions are recorded.
Managing specs within an external system such as SAP PLM? No problem. Specs managed in an external application can be synced to QualityPatrol for use throughout PatrolSuite.
Want to manage product and process specs in one place? Use QualityPatrol and configure your HMI/SCADA system to pull machine and equipment targets and specifications as needed.
“It is obvious that whoever designed this software actually worked in a QC lab. Very intuitive and easy to use.”
AuditPatrol
AuditPatrol enables internal quality, safety, environmental, manufacturing, and GxP audits to be scheduled and completed. Audit plans are user-defined, including how audit findings for each question are recorded, giving the ability to customize audit plans to fit specific needs.
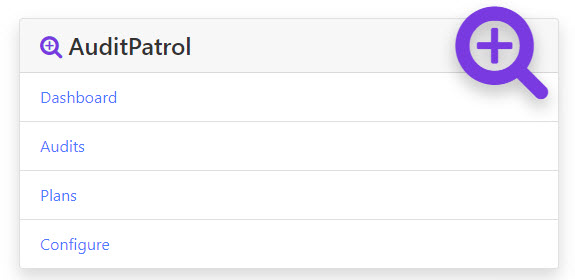
Robust security enables auditors and viewers to be granted permission to specific audit topics, and not to topics for which they are not involved.
A calendar view is provided to enable users to see audits scheduled, the nature of the audit, the Lead Auditor, and the status of the audit.
Auditors typically conduct the audits using a mobile device (tablet or cell phone) where they are guided through the necessary questions and are able to record their findings with a click of a button. Evidence can be documented, scores can be assigned, files can be uploaded, and the auditee can even document a response to the auditor’s findings. An audit report is automatically generated, and it can be filtered to see items marked for follow-up or marked as improvement opportunities.
“This gives us the ability to conduct the same audit at each plant and see which plants are performing best, and which plants need to improve.”
CertPatrol
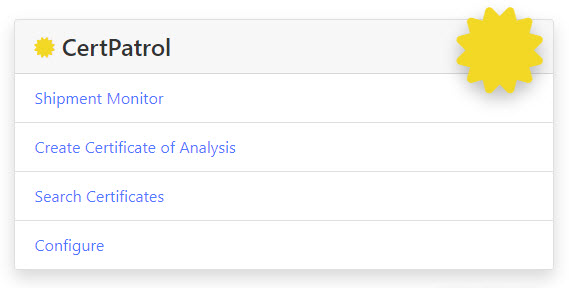
CertPatrol facilitates the management of certificate of analysis requirements at six levels: corporate master, product group, product, customer, product group/customer, and product/customer.
Multiple CoA types and over 25 different options for displaying content such as the purchase order number, manufacturing date, unit numbers, specs, etc., on each CoA, enables the production of a CoA that provides each customer with the information they need. CertPatrol also allows the definition and management of CoA recipients for each customer, ensuring that the CoA is delivered to the correct party.
Shipment Monitor is integrated with your MES outbound delivery information to advise the QC lab when a CoA needs to be created. Because the CoA requirements are pre-defined, a CoA can be created in seconds.
Does your US headquartered organization have a plant in Germany that needs to send a CoA to a Spanish speaking customer in Madrid? No problem. When the plant in Germany creates the CoA, CertPatrol will automatically produce it in three languages: English (the corporate language), German (the language of the manufacturing facility where the product was made), and Spanish (the language of the customer).
“CertPatrol reduced the amount of time I was spending creating CoAs from over 2 hours a day to about 10 minutes.”
ComplaintPatrol
ComplaintPatrol facilitates documenting, investigating, quantifying, correcting, and responding to customer complaints. Root cause analysis, risk assessment, and health/safety impact are assigned to task leaders. Corrective, preventive, and validation actions are defined and assigned, with due dates, based on the investigation findings.
User defined complaint categories and subcategories provides insightful metrics and reports. ComplaintPatrol is not limited to only product complaints, it is intended to also be utilized for complaints related to services, delivery, paperwork, packaging, and even price.
An integrated, and configurable, approval process can be initiated at multiple steps of the complaint workflow. A detailed quantification of the costs of poor quality is also incorporated into the resolution process.
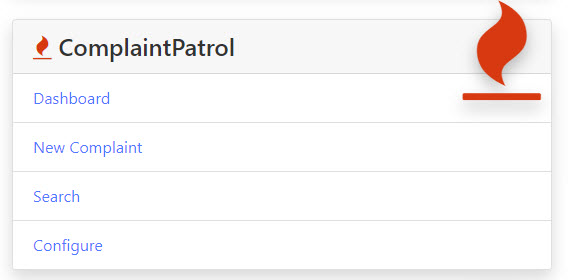
All documents, files, and images associated with the complaint can be uploaded for easy access by the investigator and approvers.
With the click of a button, users can view and access other complaints related to the applicable manufacturing order, product, customer, and the specific customer/product combination.
Remediation actions requested by the customer are recorded, as are approved financial remediation amounts, which can be synchronized with your ERP credit memo process.
An 8-discipline-based investigation report is automatically created to provide a professional response to customers. ComplaintPatrol provides the ability to document two versions of the investigation summary: one for an internal audience, and a cleansed version suitable for an external audience, which appears on the report.
“ComplaintPatrol has reduced our days-to-close because the information is so well organized and the electronic approval routes are so easy for our managers to use.”
DashPatrol
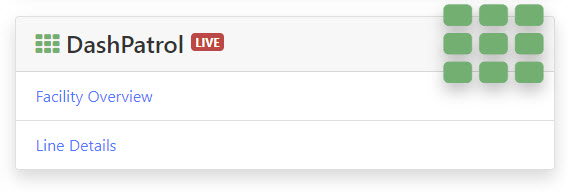
DashPatrol provides a real-time dashboard of the manufacturing and quality process. Providing real-time visibility into the manufacturing process, and implementing SPC if you choose to do so, has never been easier. The plumbing is already done. Just check a checkbox within the quality plan to define which items require monitoring.
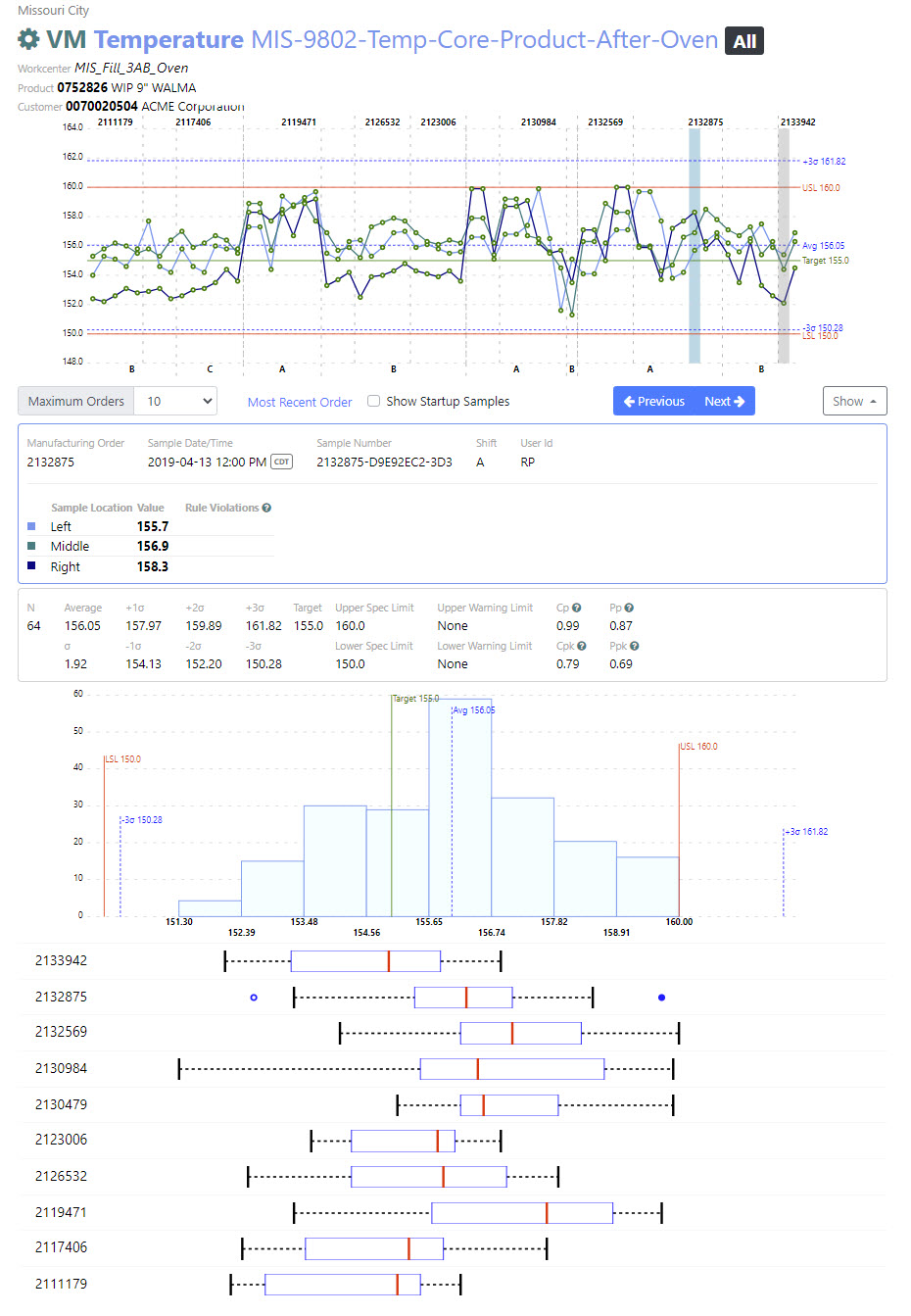
The facility overview page is designed to provide corporate and plant managers a real-time view into what products are being manufactured at each plant, and the current quality level of the product.
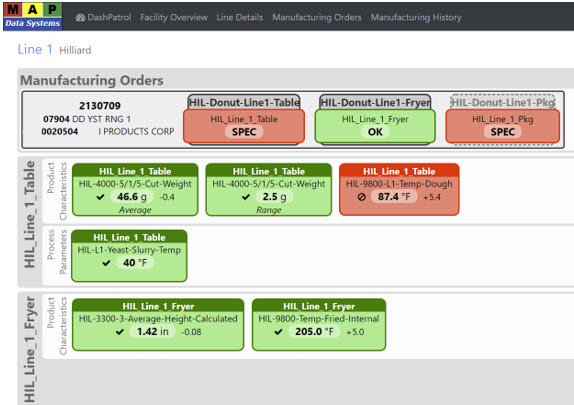
The line details page is designed to enable the shop floor operator to monitor all the critical-to-quality product characteristics and process parameters. Click on an alarm button to access the related control chart and capability histogram.
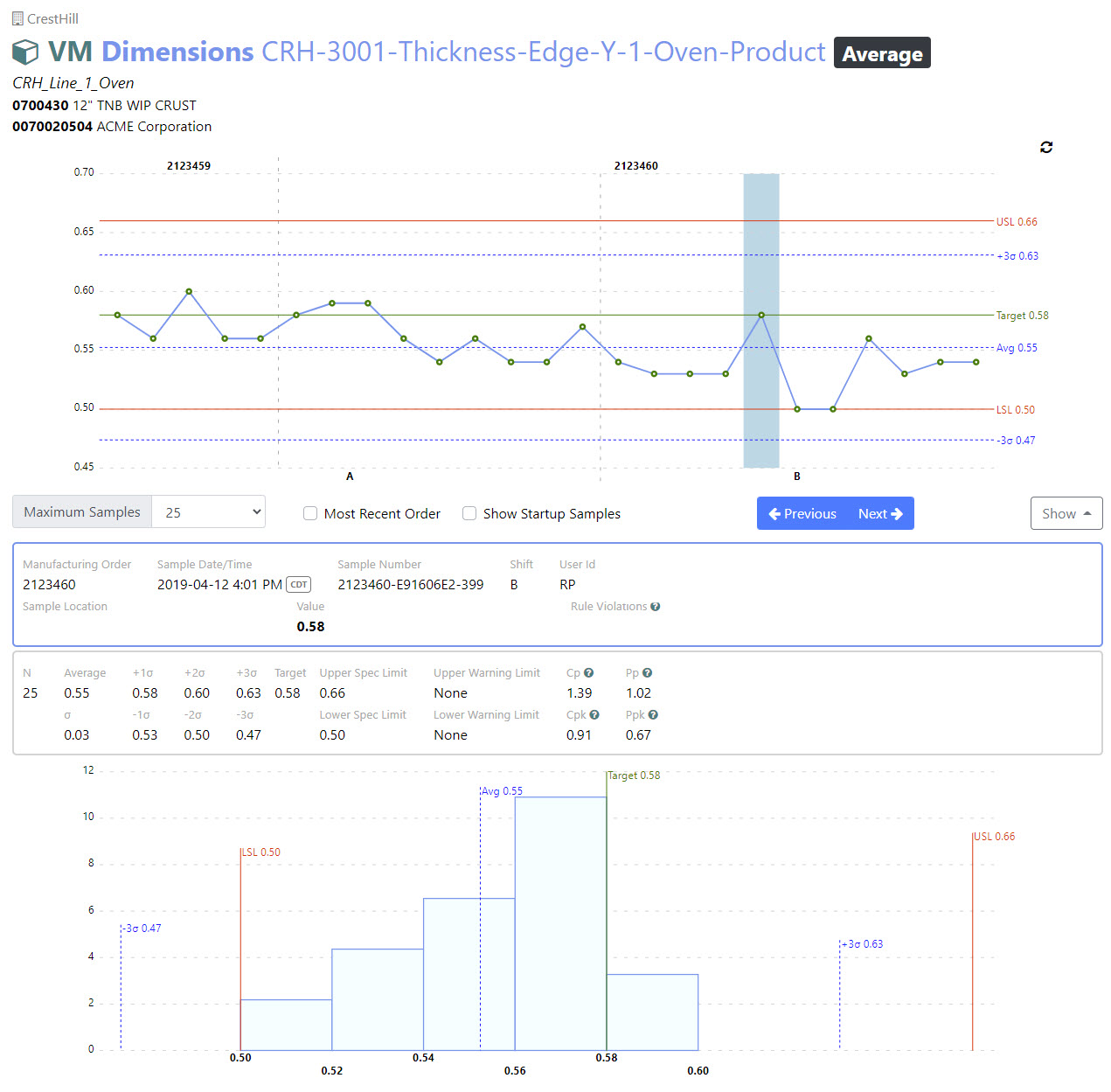
When a new manufacturing order is started, DashPatrol automatically displays the data from the previous orders of the same product, produced on the same manufacturing line, within the control charts so the operator can make decisions about setpoints and monitoring needs. The control chart page can be customized by the user to turn display settings on and off.
Pattern rules can be turned on/off by facility and test method giving finite control over the introduction of SPC.
The SPC charts are rendered in scalable vector graphics which makes them crisp and clear when viewed via a mobile device, including something as small as a cell phone.
“DashPatrol provides better visibility into our manufacturing process than our HMI/SCADA system.”
DataPatrol
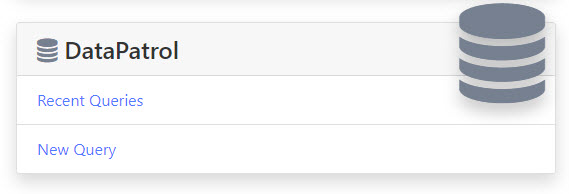
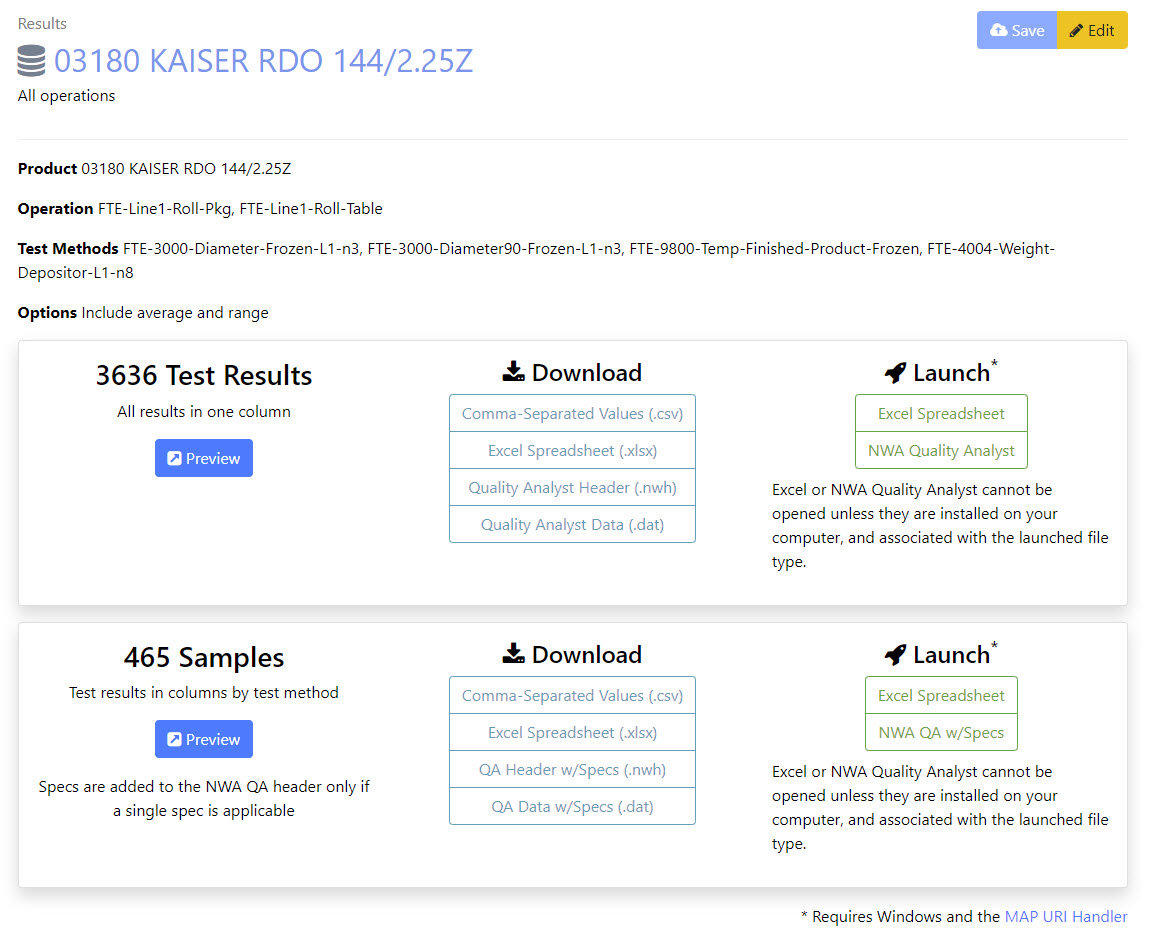
DataPatrol enables data within QualityPatrol to be extracted for analysis in other third-party tools such as Minitab, NWA Quality Analyst, or Excel. Queries that are run frequently can be saved by the user for efficient re-use. Multiple output formats provide options to make external analysis easier. A URI handler is provided to open data sets directly into Excel.
“The point-and-click filtration interface makes it easy to query the exact data I want.”
EventPatrol
EventPatrol is a centralized action management module that facilitates the investigation, root cause analysis, risk assessment tasks. Based on the results of these tasks, actions can be proposed, assigned, approved, and implemented. Actions may include containment, safety, correction, corrective, preventive, and verification/validation.
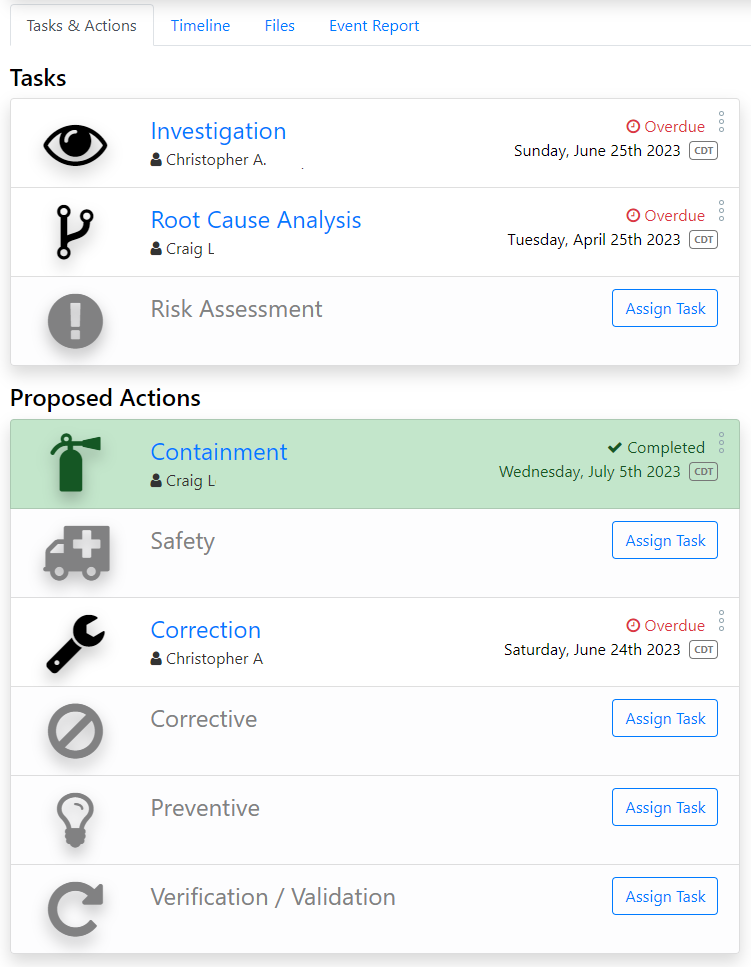
EventPatrol is integrated with ComplaintPatrol and AuditPatrol so that users solve problems using the same tool (EventPatrol) regardless of where the event originated. Additionally, non-audit and non-complaint events such as safety violations or nonconforming product can be originated and processed directly from within EventPatrol.
A robust approval system allows approval roles and routes to be user-defined. The approval systems is also centralized so that approval routes can be defined once and then consumed by any module.
An 8-D based event report is automatically generated as the tasks and actions are defined and completed.
Metrics & Reports
Visibility
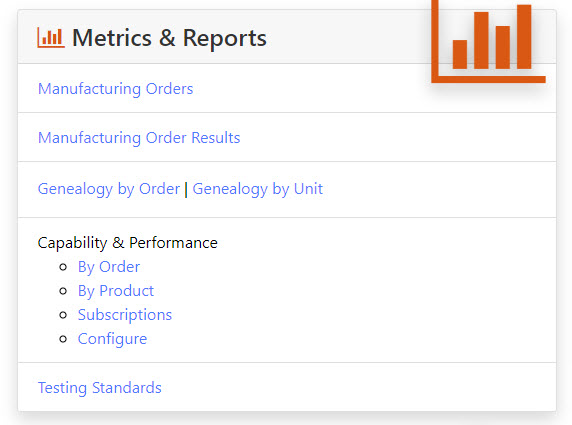
Metrics & Reports provide actionable information to users with process improvement responsibilities. The manufacturing order results page allows users to review the results of a manufacturing run of interest, with the ability to quickly identify those test methods with results that are out of specification (“excursions”). One click reveals the SPC chart for a desired test method, which provides the ability to look back in time at previous manufacturing orders of the same product. Box and whiskers charts enable the user to compare the performance of those previous orders.
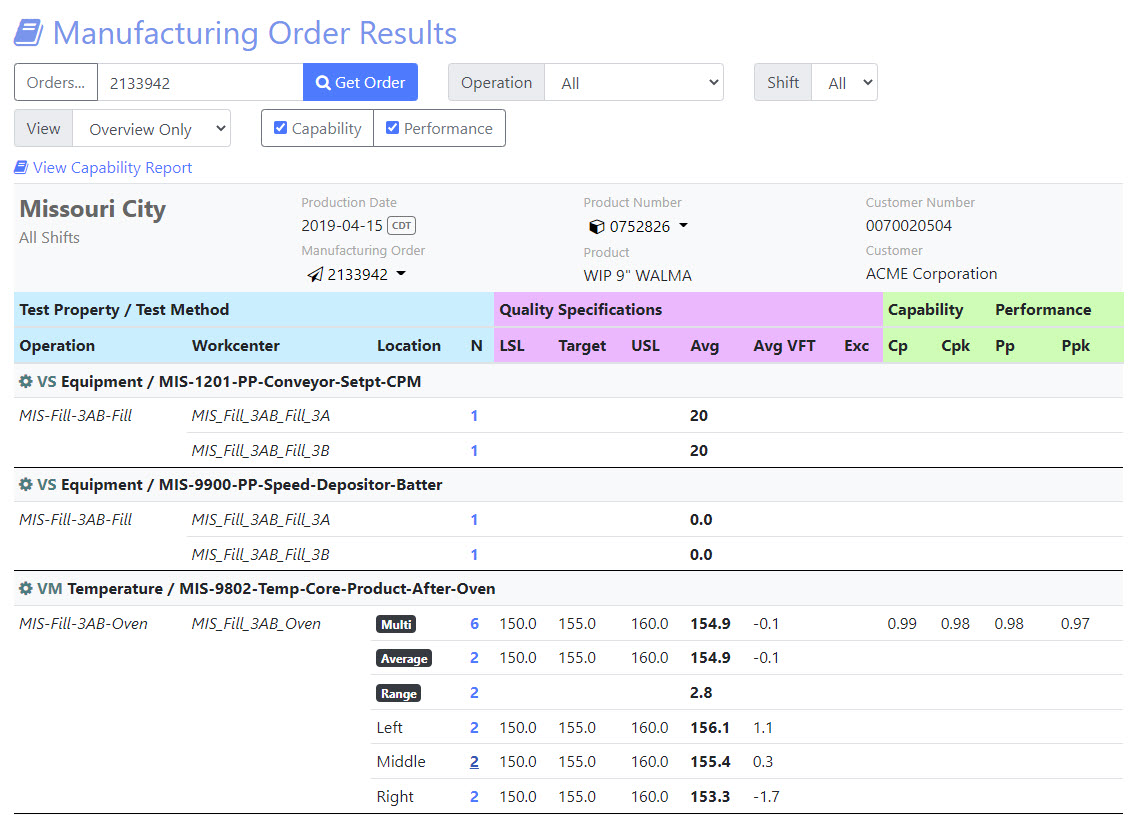
Manufacturing performance reports contain hyperlinks that allow for an efficient deep-dive into related information. For example, the capability & performance report for a manufacturing order contains a hyperlink to view a more detailed report for all orders of product ‘X.’
“We never had this kind of visibility into our products. We have learned more about our products in the past two months than we did over the past 10 years.”
Capability & Performance
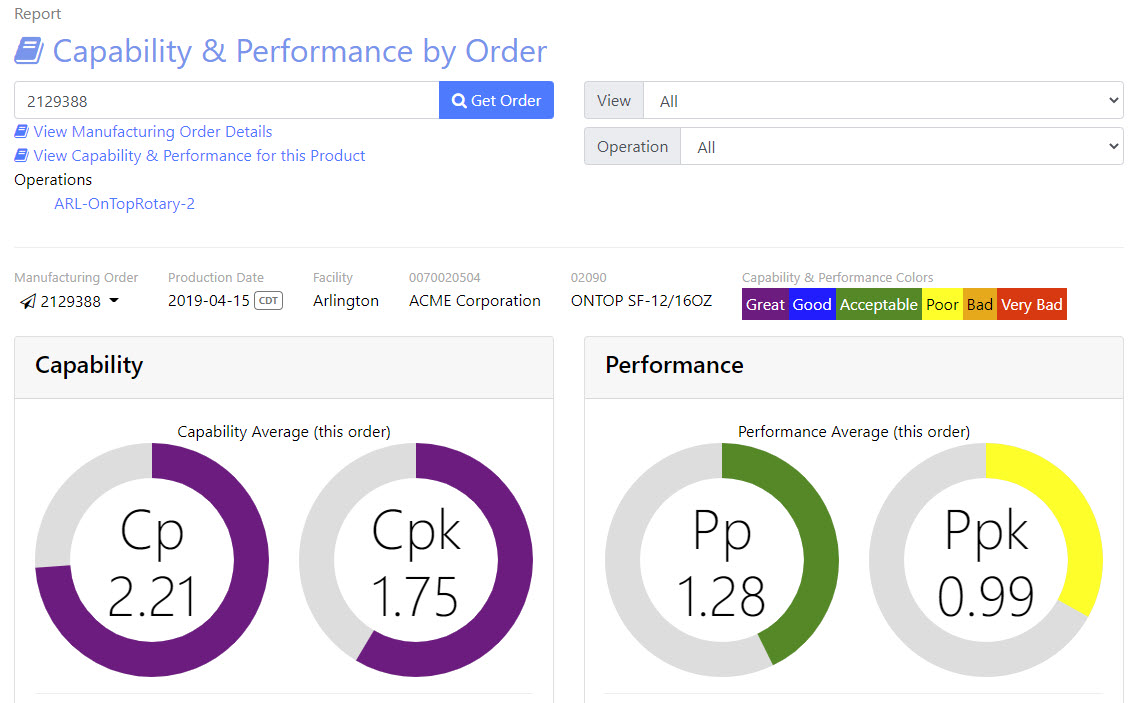
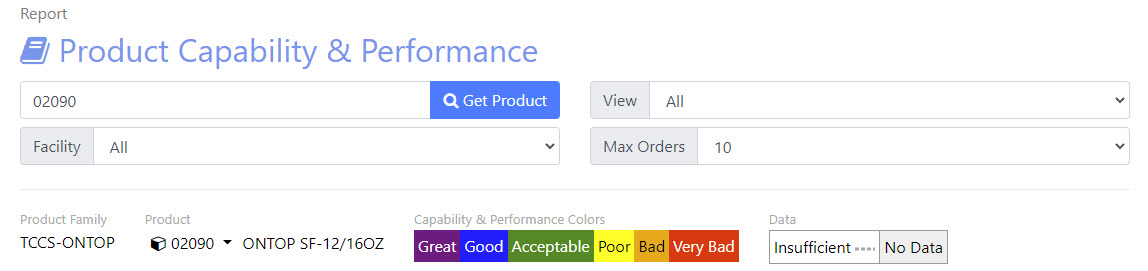
Large manufacturers often have product design and development personnel housed at a centralized location that, unfortunately, is not located near the manufacturing sites. This distance creates a barrier between the product design owner and the manufacturing results. Problem solved. The capability and performance reports are subscription based, allowing users to subscribe to products of interest. When a manufacturing order is complete, the subscribed user receives a notification that an order has been made. A hyperlink takes the user to the capability and performance report for that order.
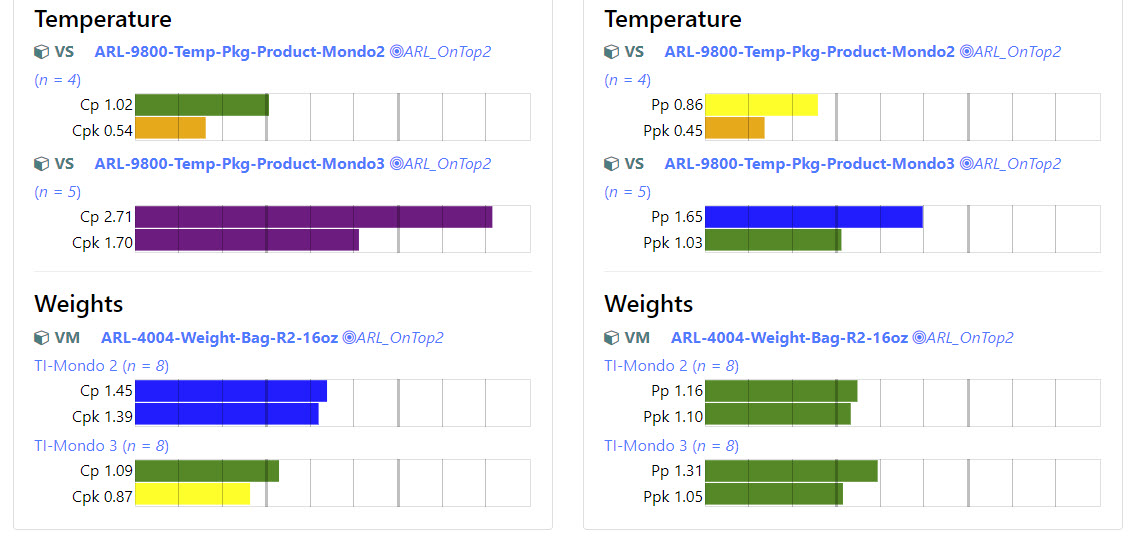
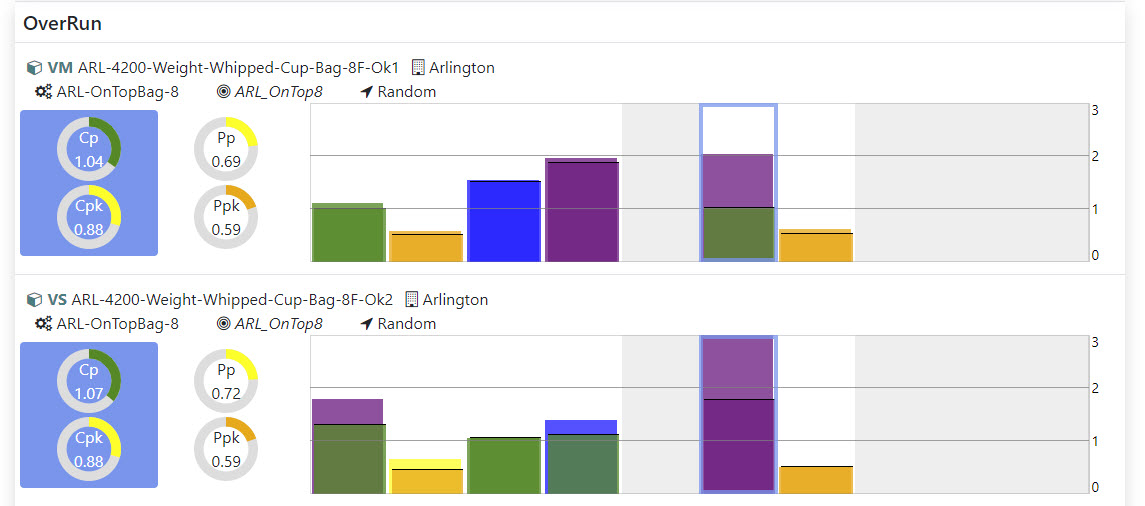
Genealogy
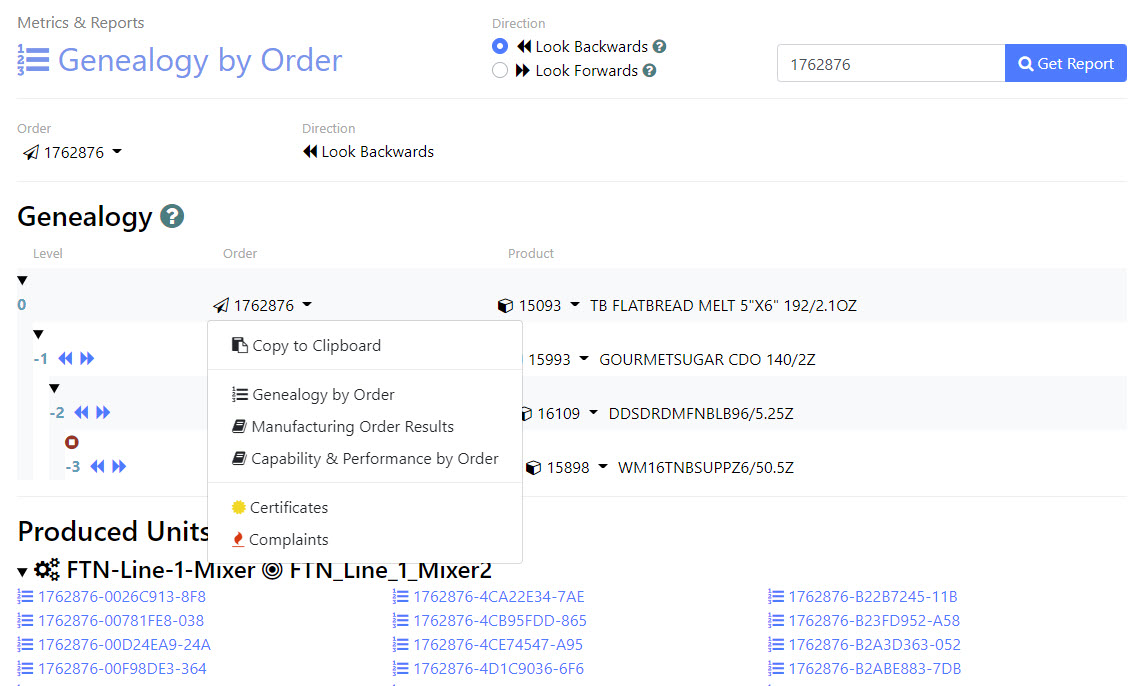
Genealogy is tracked in QualityPatrol for the purposes of producing CoAs when CoA-appearing tests are performed several steps upstream from the finished product manufacturing step. Genealogy data can also be synced from the MES. Either way, MAP has set the gold standard for how a genealogy report should look and function.
“I have been in the MES business for 20 years, and this is the best genealogy report I have ever seen. Our own report does not come close to this.”
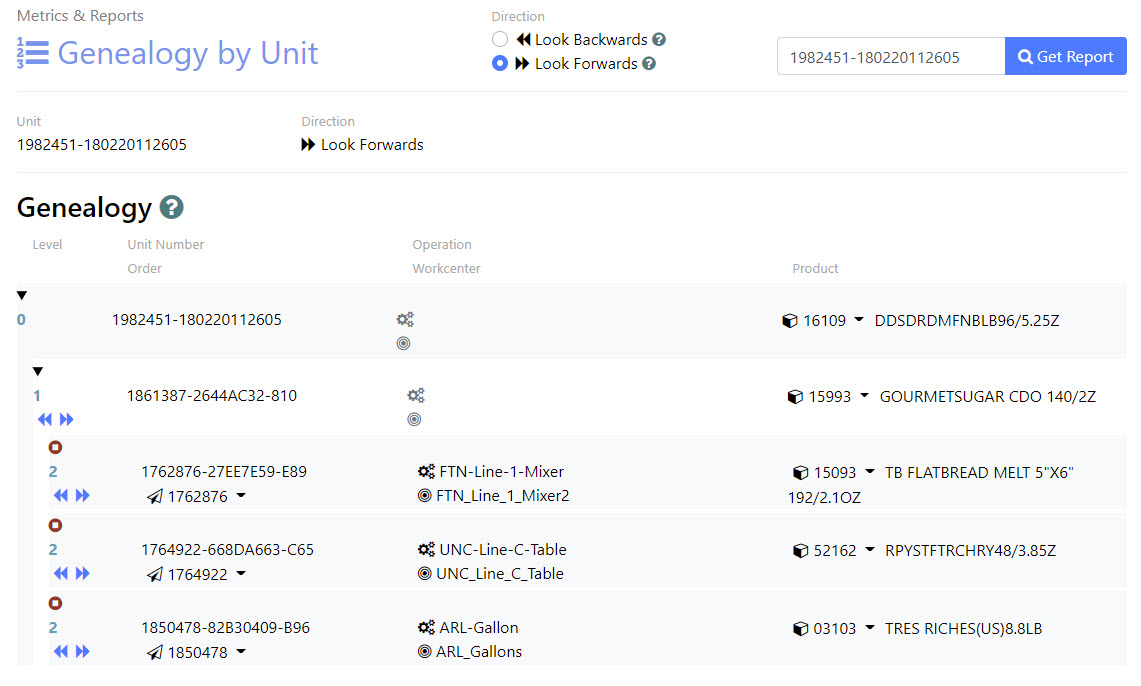
Aside from look and feel, the problem with MES-based genealogy reports is that they do not enable the user to quickly navigate to quality information. PatrolSuite solves this problem with two reports, genealogy by order and genealogy by unit, which both enable backwards and forwards views, that provide hyperlinks to each step of the manufacturing process and to each unit produced at each step. Additional hyperlinks take the user directly to the manufacturing and quality reports outlined herein and any applicable CoAs and related customer complaints.
“This report is a huge time saver when investigating nonconforming product and customer complaints.”